Aberdeen Technologies is a trusted medical device injection molding company, providing cost-effective, high-precision plastic components that meet strict regulatory standards for the healthcare industry.
What is Medical Injection Molding?
Medical injection molding is a manufacturing process that produces plastic medical devices and components. It involves melting plastic resin pellets and injecting the molten material into a mold to form specific shapes. This method allows for precise control over size and shape and adheres to strict quality and regulatory standards.
It's capable of producing FDA-approved devices that are both durable and reliable, and it's also ideal for prototyping as part of the FDA approval process. Injection molding can be performed in a cleanroom environment, and the components can be sterilized without compromising their integrity.
Advantages of Injection Molding
Injection molding is a common method to form plastic parts with tight tolerances. It is widely used across industries including medical, automotive, and consumer electronics.
Medical molding can be done in clean rooms, and parts can be sterilized safely.
Materials Used in Medical Injection Molding
Medical insert molding typically uses thermoplastics which are materials that can be melted, injected into a mold, and cooled into precise shapes. Theses molds can range from simple to highly complex, depending on the part’s design.
Thermoset plastics are also occasionally used but are less common in medical molding due to their non-recyclable nature.
Assembly and Insert Molding
In medical manufacturing, it’s common to combine metal and plastic components. This process is called insert molding, and it’s frequently used to produce items like needles, EKG hookup leads, and other complex medical devices.
Our Expertise in Medical Injection Molding
At Aberdeen Technologies, medical injection molding is our core competency. We help healthcare companies bring innovative devices to life from early concept and prototyping to full-scale production.
As an experienced insert molding manufacturer, we are ISO 9001:2015 certified and often work with teams during early development stages, molding parts for clinical trials and marketing evaluations.
Seamless Transition to Production
Once prototypes are approved, we guide clients through the transition to production. With over 700 square feet of ISO certified cleanroom injection molding space, we can accommodate both low- and high-volume runs while maintaining strict quality standards.
Complex Projects, Delivered with Precision
Our capabilities include:
- Molding non-communicating passageways through plastic manifolds
- Producing critical-tolerance pacemaker components
- Molding around delicate materials like glass without causing damage
With advanced equipment and expert staff, we tackle even the most technically demanding projects.
End-to-End Manufacturing Support
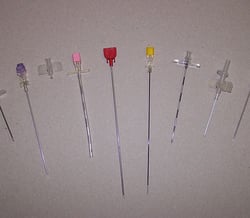
We support your project through every phase:
- Design consultation
- Mold tooling fabrication
- Prototyping and first article approval
- Process validation
- Full-scale production
- Turnkey system transfers, if needed
Typical Medical Applications We Support:
- Multi-Purpose Medical Needles
- Multi-Lumen Catheters
- Male/Female Luer Locks
- Trocar Handles
- Scalpels and Other Instruments
- Pacemaker Components
- Filters
- Patient Electrodes
- Fetal Monitoring Probes
- EKG Hook-up Leads
- Y Connectors
- Power Cords
Contact us today to recieve a same-day quote, or learn more about our other services: